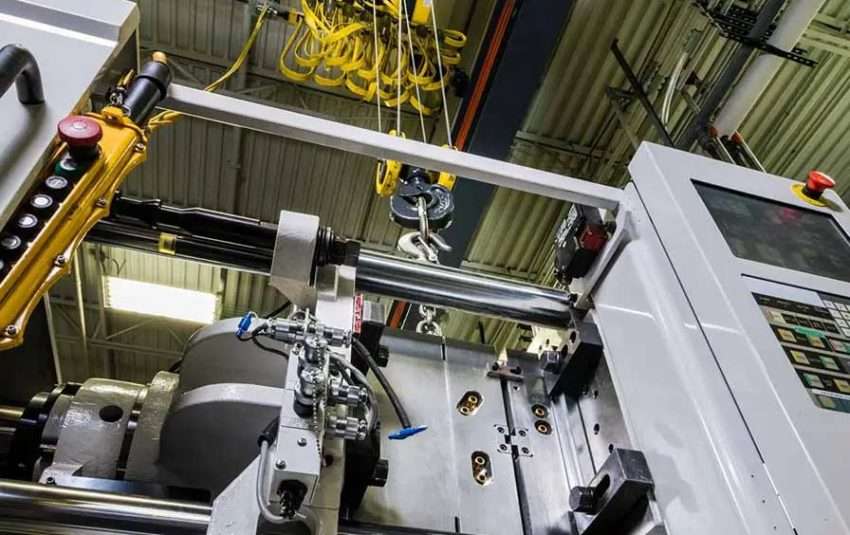
The auto industry is under constant pressure to improve fuel efficiency, reduce weight, and boost reliability. That means cutting metal where you can, tightening tolerances, and eliminating unnecessary waste. Injection molding helps you do all three. Once your mold is perfected, you are off to the races. You can run tens of thousands of units with minimal deviation.
Here is what makes the process a strong fit:
- High-volume output with consistent quality
- Tight tolerances and repeatable dimensions
- Material flexibility to meet safety, heat, and wear standards
- Low scrap rates compared to machining
- Efficient tooling for complex shapes
What Makes Automotive Injection Molding Different?
Not all molding jobs are created equal. When you are molding a part that has to survive vibration, heat, UV, chemicals, or freezing temperatures, there is not much room for error. Add in functional requirements like threading, strength under torque, or integration with metal inserts, and things get technical fast.
Automotive-grade injection molding focuses on more than just appearance. It is about structure, function, and endurance over time. These are not low-stress parts. Many are load-bearing, heat-exposed, or part of the vehicle’s safety and mechanical systems.
Typical Parts Molded for Automotive Use
Some of the more common parts include:
- Interior trims (panels, bezels, dashboard components)
- Bumpers and grilles
- Housing for electrical units
- Fluid reservoirs
- Air intake components
- Under-the-hood fasteners and brackets
Tooling Matters More Than You Think
A good injection-molded part starts with a great mold. And in automotive, the mold has to do a lot more than shape plastic. It has to handle tight tolerances, high pressure flow, and often integrate sliders, lifters, or hot runner systems. Tooling design directly affects:
- Cycle time
- Part quality
- Dimensional stability
- Ease of assembly downstream
- Scrap rates
If a mold is slightly off or vents are poorly placed, it can lead to flash, warping, voids, or weak spots. If there is inconsistent cooling, you will have shrinkage. These are not just cosmetic issues, they affect how parts perform over time, especially when exposed to real world stress.
Upfront tooling costs are high. But with proper design, you reduce unit cost drastically over long runs. Many auto parts run in the hundreds of thousands before molds need refurbishing.
Material Selection Is Key
You can’t mold automotive-grade parts with just any resin. The material has to handle your specs for strength, temperature resistance, wear, and chemical exposure. Resin selection also affects how the part flows during molding, which changes the design tolerances and gate placement. Here are a few resins commonly used in automotive injection molding:
- Polypropylene (PP) for interior trim, battery cases, fluid tanks
- Nylon (PA6, PA66) for engine components, gears, housings
- ABS for dashboards, panels, and interior bezels
- Polycarbonate (PC) for lenses and transparent covers
- PBT and PET blends for electrical connectors and sensors
Many resins can also be glass-filled or reinforced to meet impact and strength requirements. If a part needs to work alongside metal or withstand mechanical load, you will likely be working with reinforced polymers.
The Process From Mold Design to Final Part
Injection molding follows a predictable process, but every step matters if you are aiming for top tier automotive performance.
- Part and Mold Design
You start with the CAD model of the part. Engineers tweak wall thicknesses, ribs, and radii to improve flow and avoid weak spots. Then mold makers design steel or aluminum tooling that matches the CAD exactly.
- Mold Fabrication
Precision CNC machining creates the mold blocks. These are fitted with runners, gates, vents, ejector pins, and cooling channels. This phase takes time, but it is critical.
- Molding Trials
Once the mold is built, trial runs begin. You will test different shot sizes, temperatures, and pressures. Part measurements are verified with CMM equipment. It’s a lot of back and forth, but it ensures the part performs under heat, vibration, and repeated use.
- Production Runs
After validation, you move into production. Shot after shot, parts are molded in seconds. Trimming, inspection, and assembly happen downstream. Real time monitoring is often used to catch any process drift.
- Post Molding Processes
Some parts require secondary steps like ultrasonic welding, metal insert installation, or surface texturing. All of these need to work seamlessly with the molded part, so it pays to plan ahead.
Quality Assurance Is Non-Negotiable
No automotive part makes it out the door without inspection. This means more than just visual checks. Look for:
- Dimensional inspection
- Strength and load testing
- Heat cycling
- Chemical exposure testing
- Surface hardness
- Impact resistance
Statistical process control (SPC) is also common. When you are running thousands of parts a day, you need to know when something drifts before it causes downtime or rework.
OEMs demand traceability, so most parts are tracked by lot, with full material and inspection documentation. Miss a step, and the whole batch can be rejected.
How Automation Fits In
Automation has become standard for many injection molding operations, especially when you are producing automotive parts with narrow margins and short lead times. It cuts down labor costs, yes. But more importantly, it ensures consistent cycle times and reduces handling damage. In a plant producing high volumes, this adds up quickly. You will often see:
- Robotic arm part removal
- In-line vision systems
- Automated trimming or part sorting
- Conveyor-based part movement between stations
Choosing the Right Partner for Automotive Injection Molding
If you are outsourcing your molding, pick a supplier who understands automotive grade quality requirements. They should be able to walk you through the design for moldability process, offer advice on resin choices, and produce consistent parts from start to finish. If they cut corners on tooling or material, you will see it in warranty claims down the line. Look for:
- ISO/TS 16949 or IATF 16949 certification
- In-house tooling capabilities
- Experience with your specific resins or part types
- Robust inspection and reporting systems
- A track record with OEMs or Tier 1 suppliers
Final Thought
Injection molding isn’t the flashiest part of automotive manufacturing, but it is one of the most critical. The process gives you control over repeatability, weight, and cost, the three things that are always under pressure in this industry.
With the right mold design, the right material, and the right injection molding company, injection molding helps you hit your production targets without sacrificing performance. For automotive parts that need to be just right, every time, it is hard to beat.